Use Cases
Modix serves a wide range of users with diverse 3D printing needs. They include professionals in automotive, film, aviation, art, and more.
Interior design
Jh Studio, based in Seoul, specializes in architecture, interior design, and more. The studio collaborate with artists to create innovative design solutions that go beyond one-dimensional project needs. Check website: link
3D Printing Farms
A farm of Modix 3D printers enhances productivity and flexibility for producing large parts. It enables simultaneous, large-scale printing, speeding up production and meeting high-volume demands efficiently. The technology’s compatibility with various materials and complex geometries allows for 3d printing service houses to provide fast service to large orders of big parts.
Vital Auto (UK) stands at the forefront of automotive prototyping, equipped with an extensive fleet of 16 Modix 3D printers, ranging from the original BIG-60 V1 to the latest GEN4 models. This enables rapid and versatile prototyping solutions for top-tier OEMs. Reflecting their distinct brand identity, Vital Auto has customized all printers in a signature yellow, showcasing their commitment to innovation and design excellence. https://www.vital-auto.com/work
Incept 3D, a leading 3d printing service from San Diego USA is renowned for its vast collection of 3D printers, complemented by a user-friendly online system that guarantees rapid project quotes and deliveries. Incept is a proud owner of several Modix printers, most are running since 2019 proving that their heavy-duty design works.
Michael Armbruster, Incept 3D CEO: “They have been amazing for our company” https://www.incept3d.com/
Automotive Body Parts
Illumaesthetic is a leading developer and service provider in the automotive after-market industry located in California, USA. Illumaesthetic develops and manufactures some of the most unique and innovative parts in the aftermarket cosmetic market and they have multiple Modix’s 3D printers to fulfill their design and service needs. Here are a few of their amazing projects, Check them on Instagram.
Specific car parts
Automotive Aftermarket
Chuck Taggart is a developer of automotive aftermarket accessories and popular YouTube channel creator (@CLTaggart).
Chuck owns two Modix’s printers including BIG-120X V2 & BIG-120Z V4. Here are a few of his works made with Modix printers.
Read article
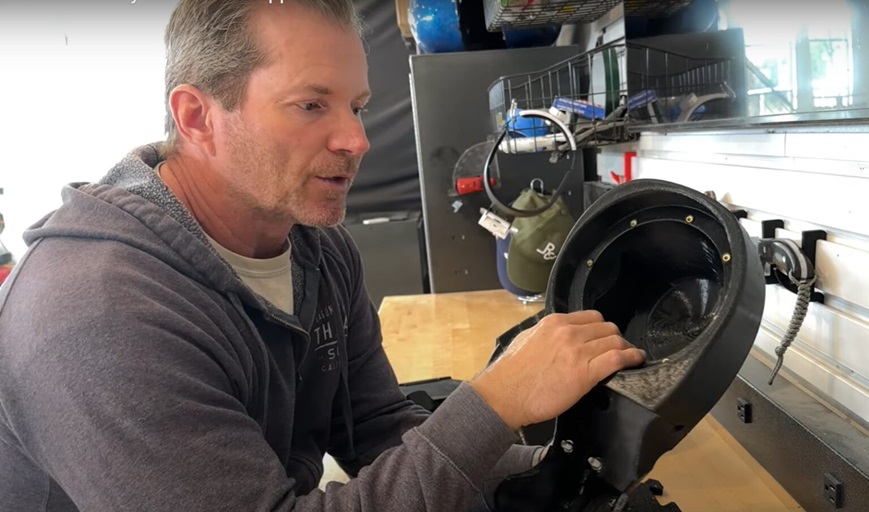
Harley lower speakers
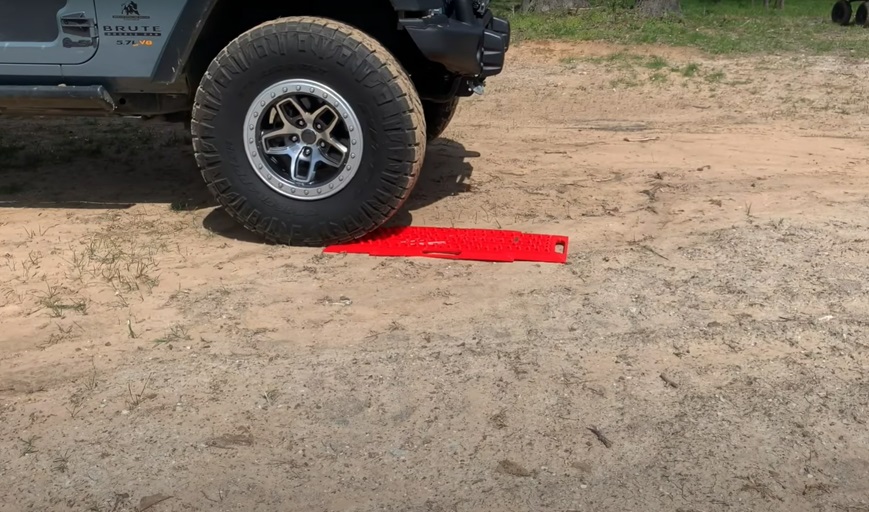
Recovery boards
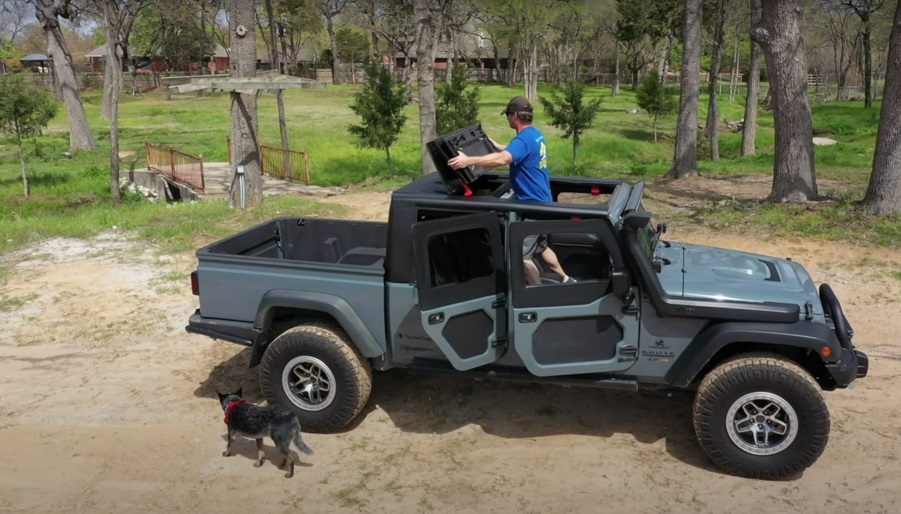
Hardtop convertible
Complete rework
Art
Bill Albertini is a New York-based artist known for his solo exhibitions at various galleries, including Martos Gallery and Alona Kagan Gallery in New York, as well as international group exhibitions. He holds degrees from the Crawford College of Art, Cork, Ireland, and the Yale School of Art. Check his website at link.
Casting
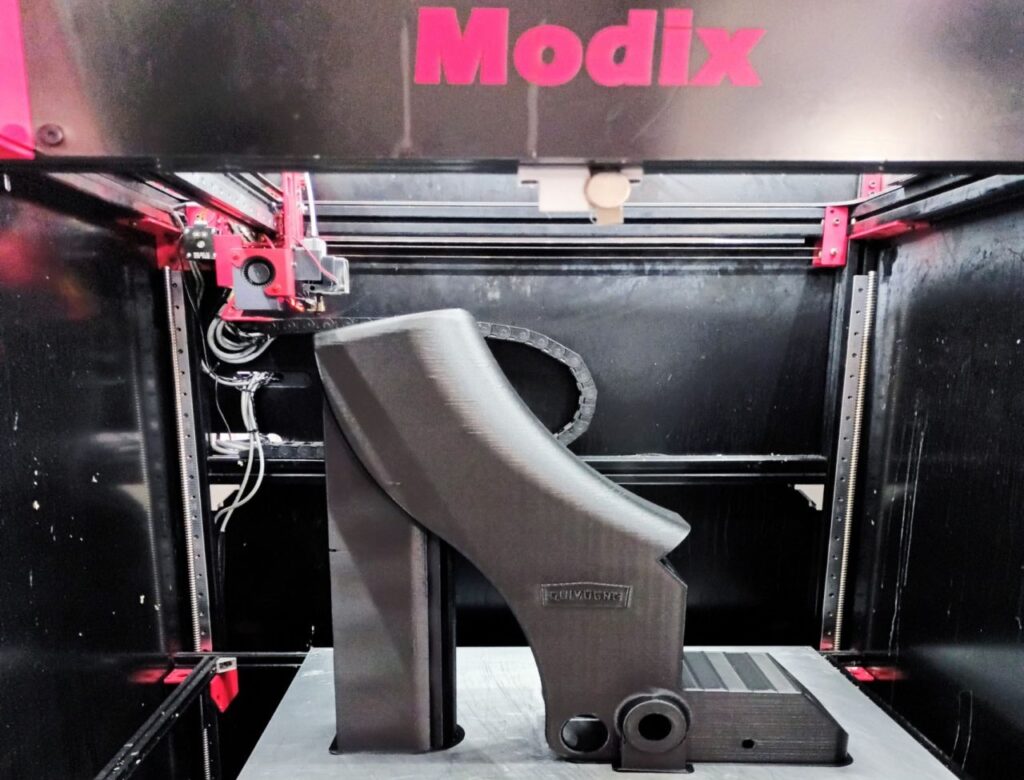
Part of foundry model for Steel casting. Peter De Corte OMD3D 3d print service, Belgium.
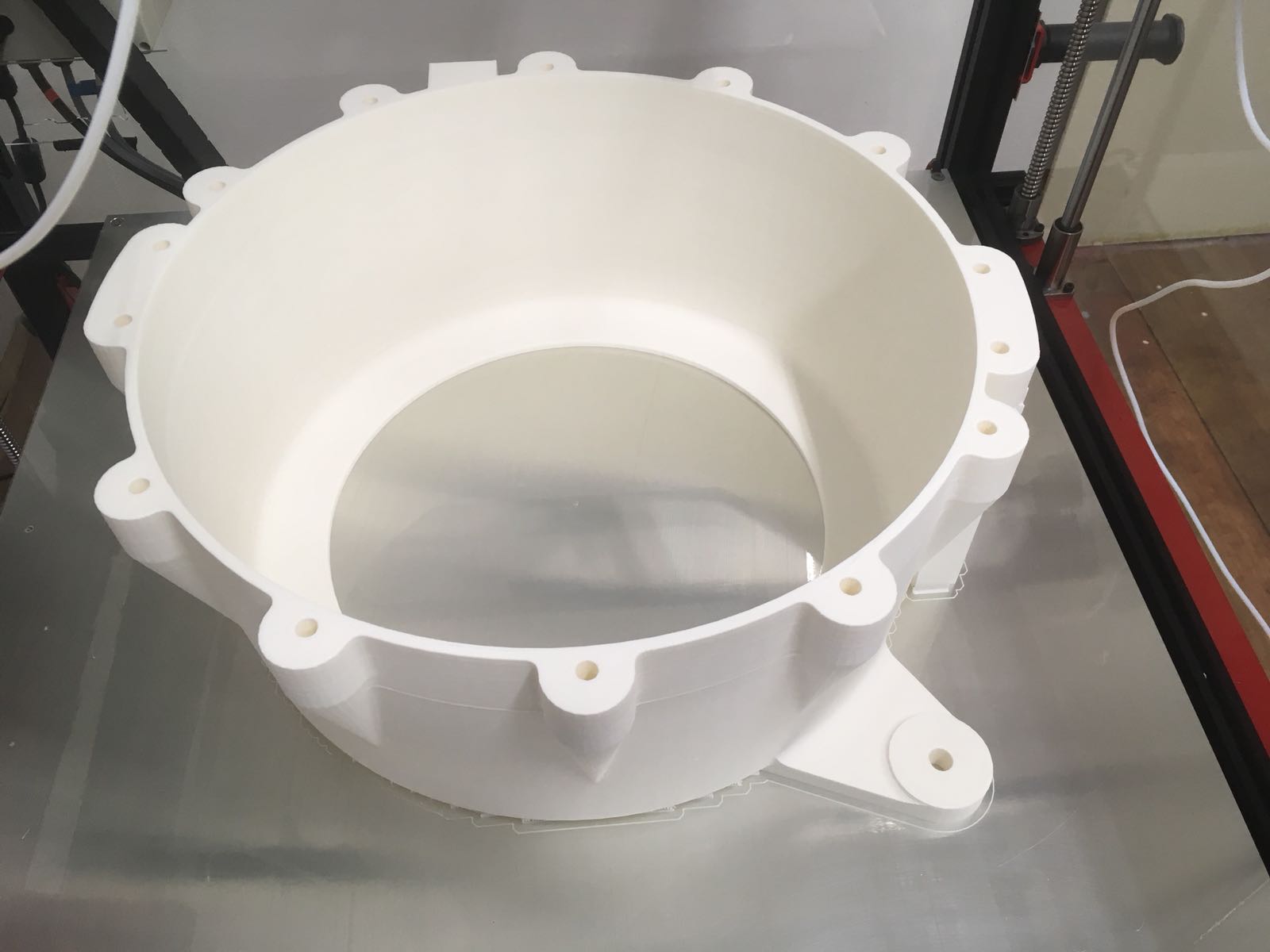
Mr. Zdeněk Horák, 3D Printing Service: F3DP – Holešov, Czech Republic: This is engine cover (two Wheeler). Printing profile: PLA, filament, speed 80mm/s, layer 0,35mm. Total print time is 38hours.
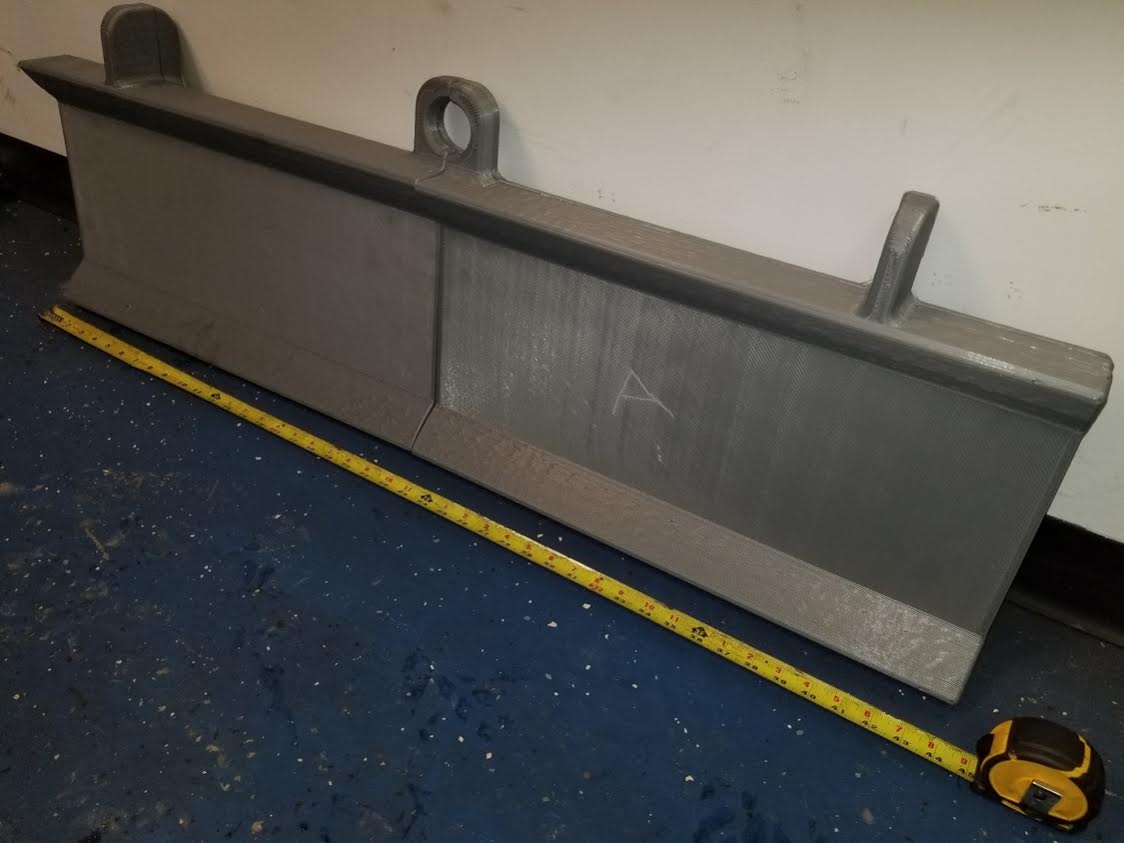
Cast steel: Canadian Construction Manufacturer: Made of two parts. Total 44″ long (” = inches) 1117mm. Maximizing the total Modix Bi60 large 3D printer build bed.
Mass Customization
Metralabs, Germany is a leader developer of mobile autonomous robots. For each of their customers they tailor the robot design. By the help of Modix BIG-60 they produce a few dozens of enclosures per each order. Alexander Kloska, Mechanical Engineer and Metralabs: “The print quality is improving with every print. We finished a robot for a new project last week. All the housing parts were printed with your printer. The parts were grinded, filled and painted afterwards. For our prototypes and small productions we normally use the 1mm nozzle and the 0.6 layer size. Each enclosure part takes approximately 20 hours to print.”
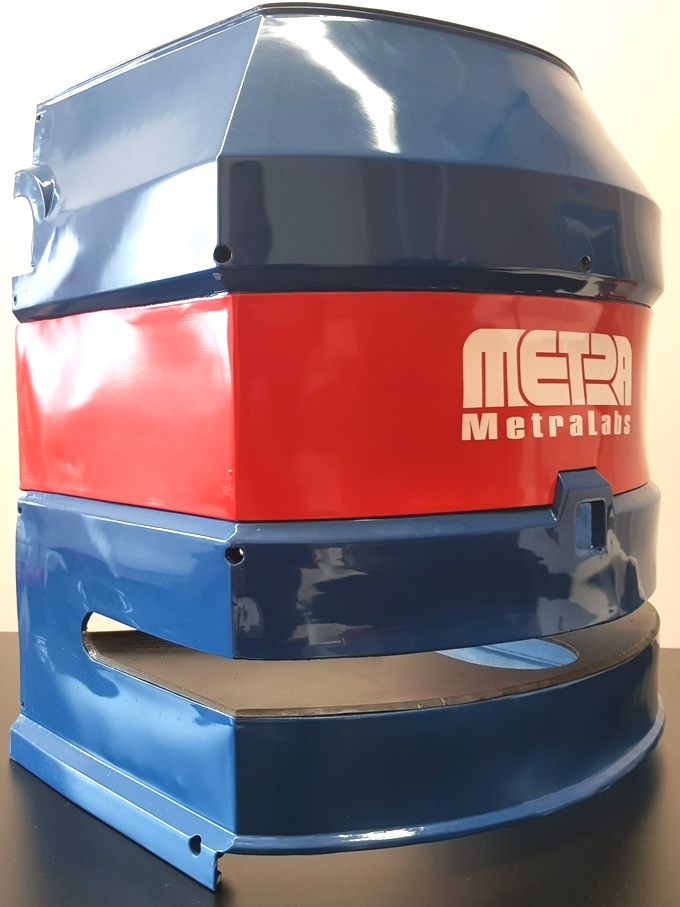
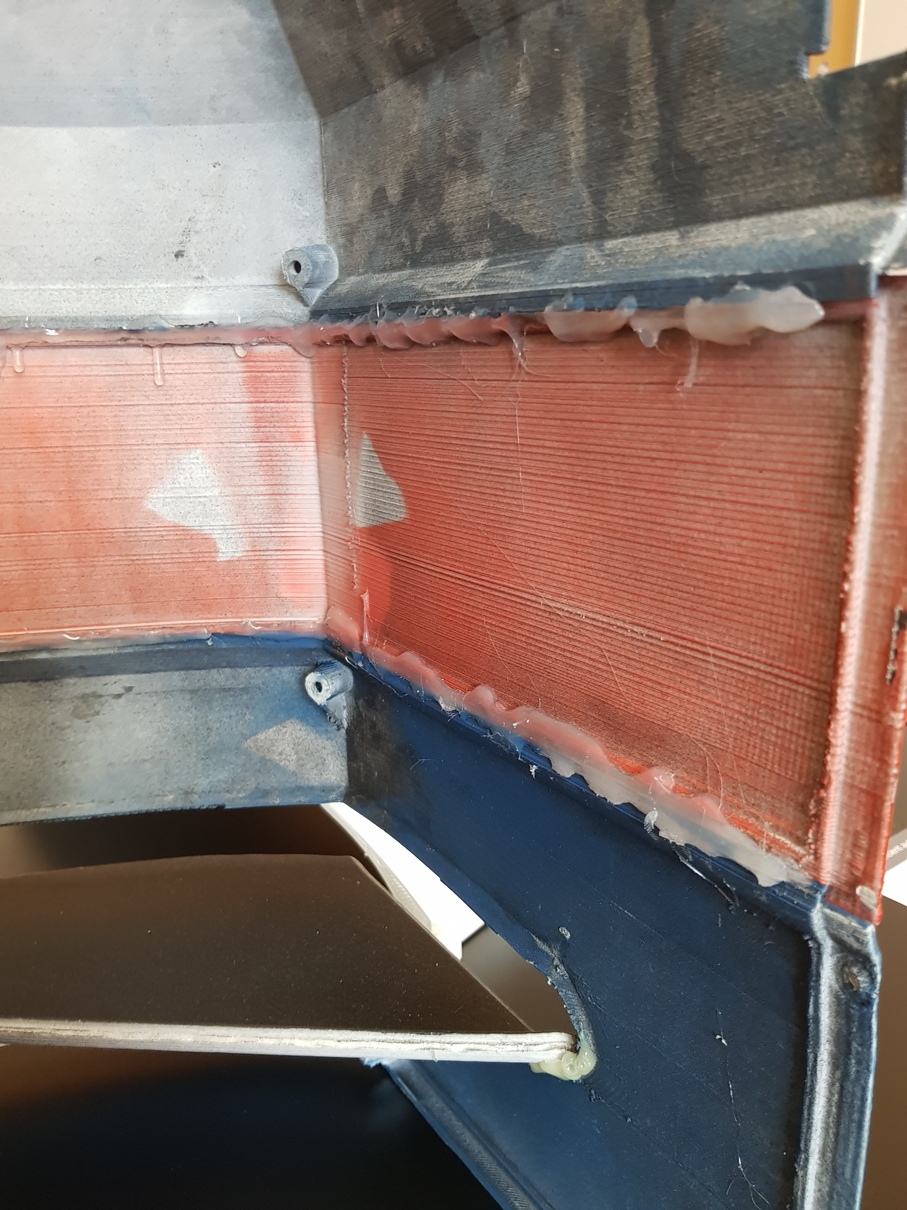
Tooling
SIM Automation GmbH is a leading automation company from Heilbad Heiligenstadt, Germany. Sim Automation has purchased a Modix Big60 3D printer in order to expedite the development of their specially designed large feeding bowls. These bowls oscillate in a special way that helps the components to climb along their grooves and feed the assembly robots in a very specific order, angle and speed. These feeding bowl prototypes are printed and then tested in a development system. Final production parts are sometimes printed with medical certified ABS filament.
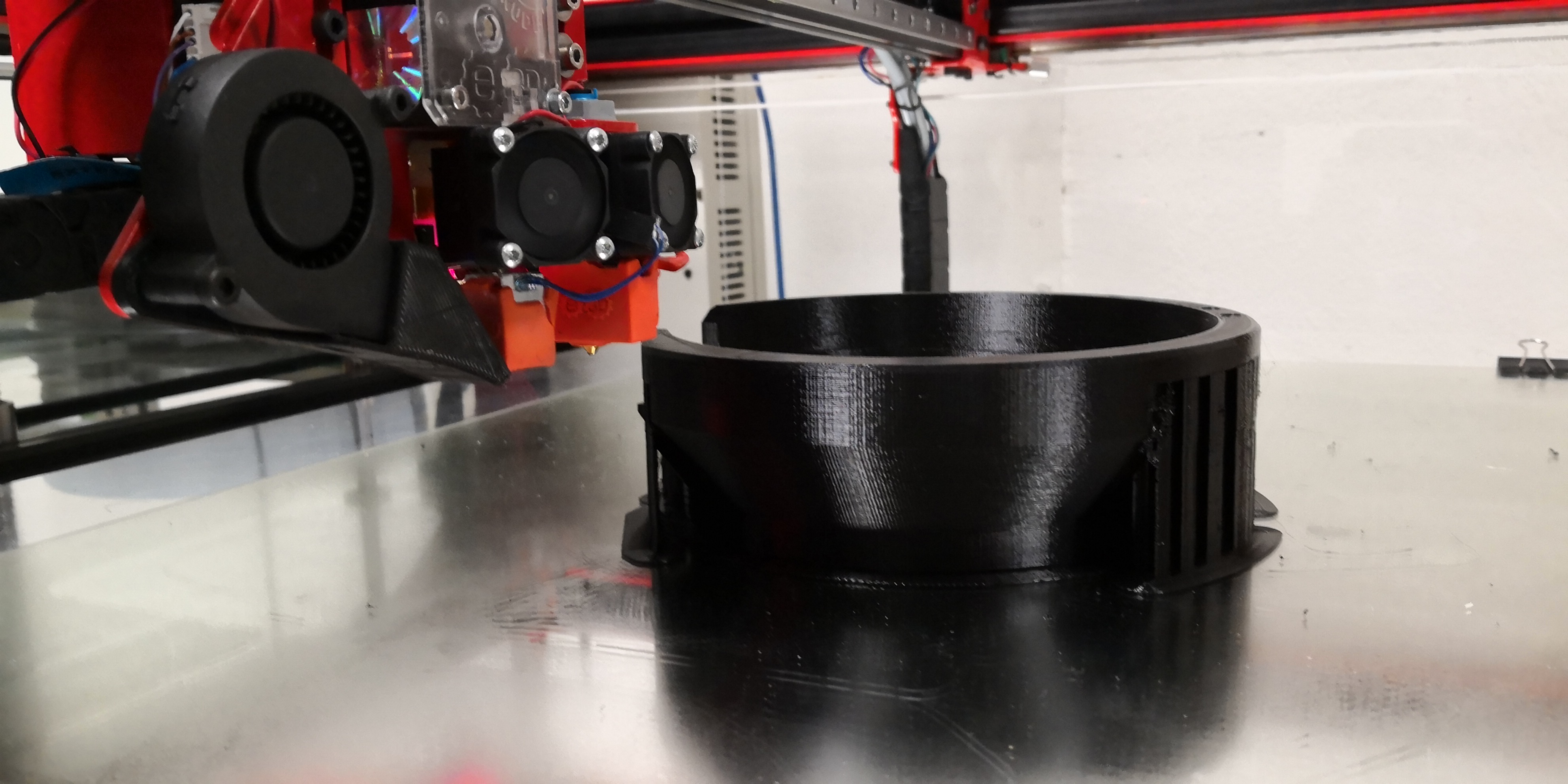

Education
For over two years Mr. Frank Chase (USA) is using Modix BIG-60 v3 in order to make it wonderful mechanical educational models.
R&D
Titan International, the owner of both Titan and Goodyear Farm Tire brands, offers a full line of wheels, tires and undercarriage products for a wide variety of off-the-road vehicles. “The printer has been doing well. We have at least 72+ days of print time on our machine and it’s still doing great. We’ve printed with PLA 100% of the time and only yesterday successfully printed a grommet for the factory using some flexible TPU filament.” Zach Pope, Tire Design Engineer, Titan International, Inc.
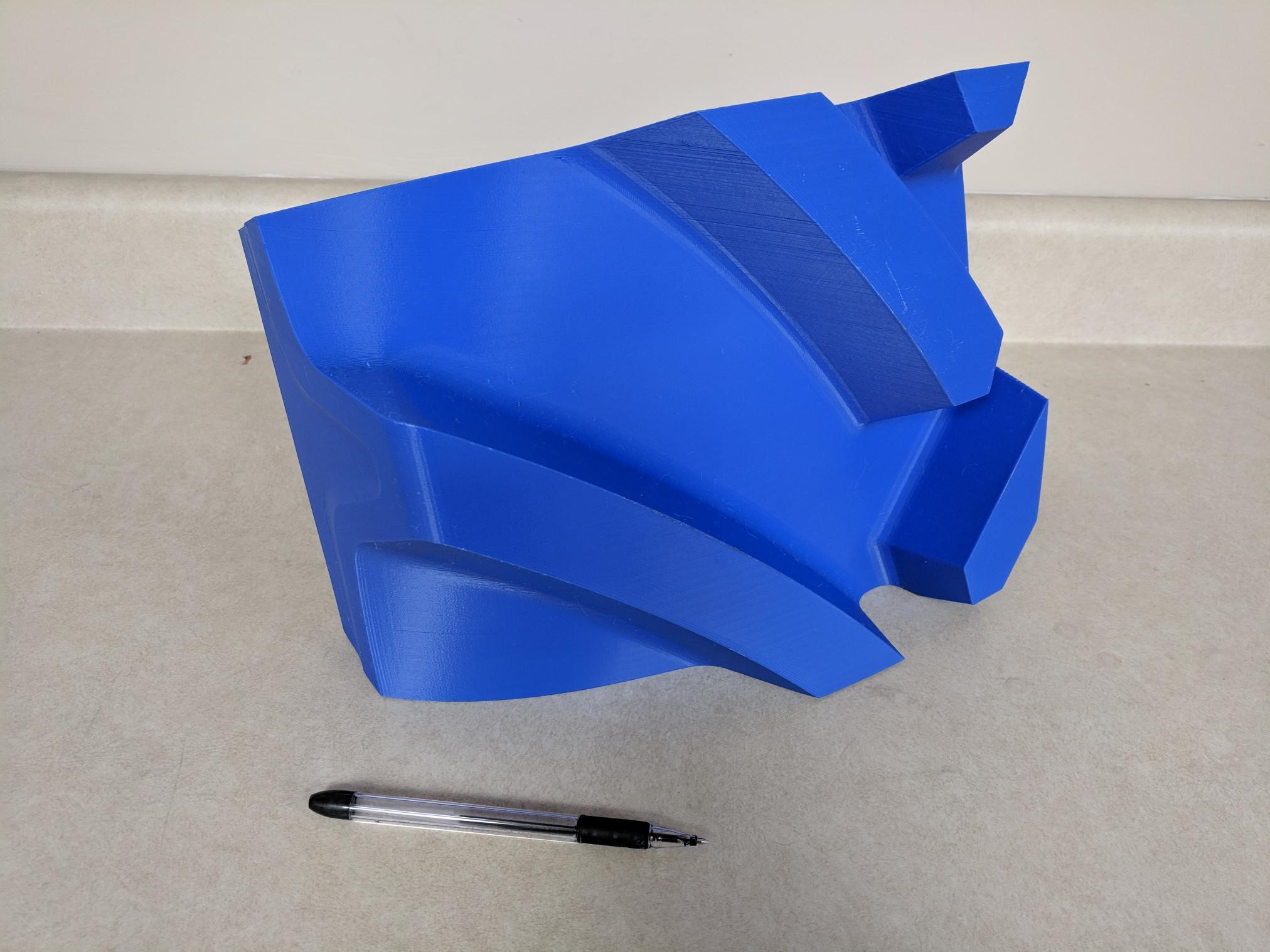
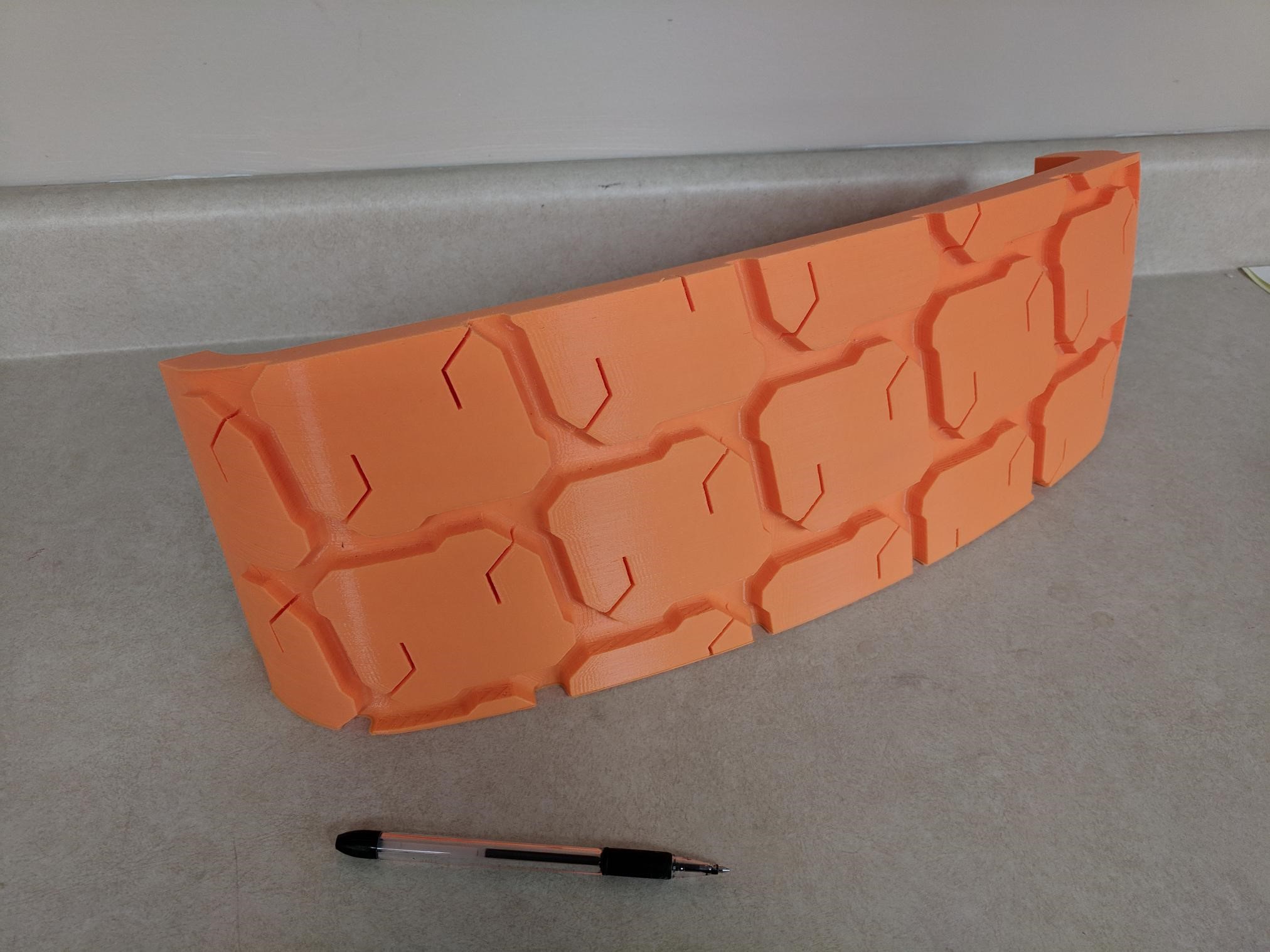
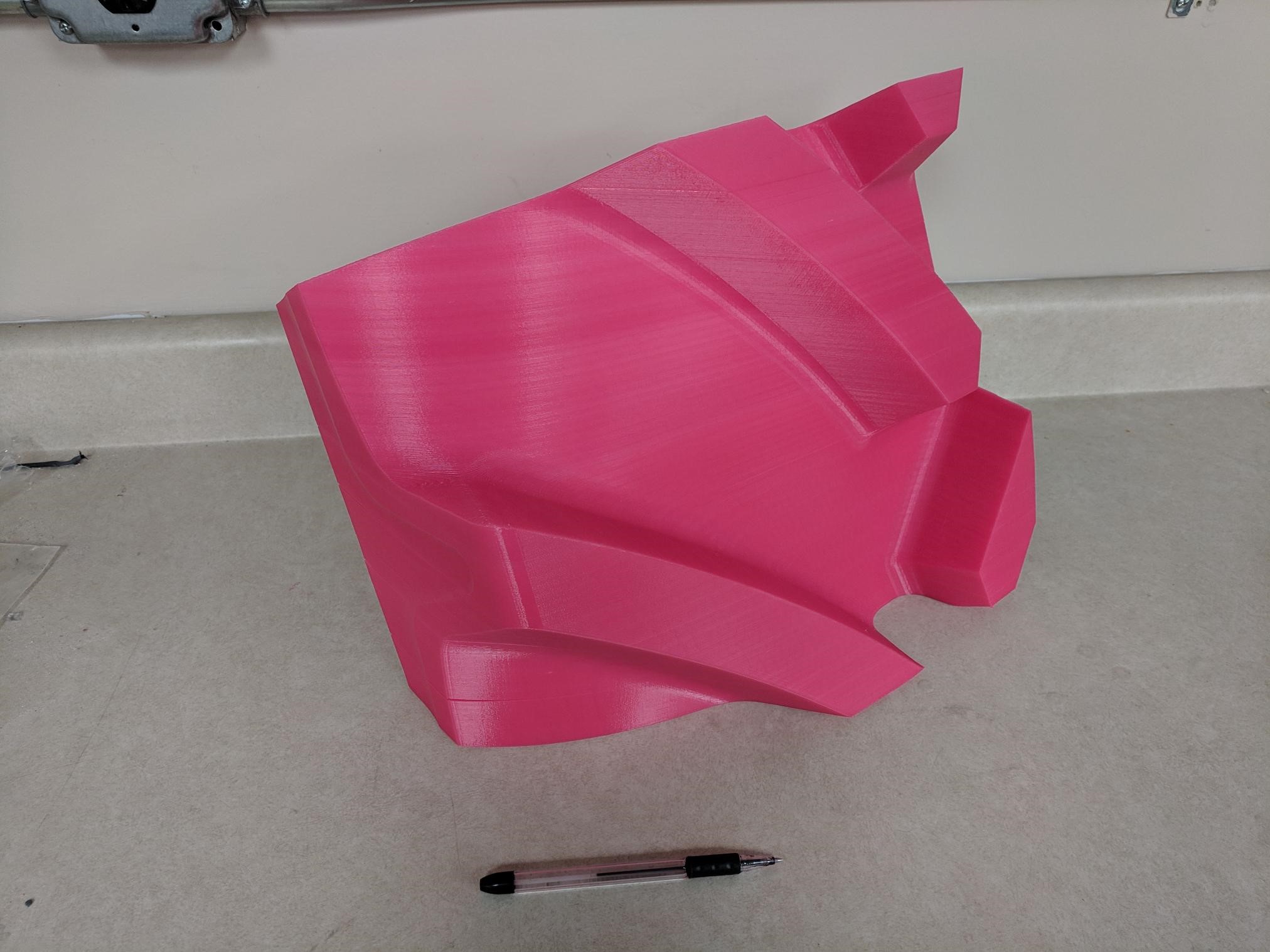
Sculpting
Mr. Patrick Laroche is a famous French sculptor using Modix 3D printer for scaling up or down is hand-work. 3D printing allows Sculptors to commercialize their work easily and faster. Rafi is a professional painter and 3D printing post processing expert service provider
from the north of Paris, France.
Films Special Effects
Shawn Hicks, Film industry special effect specialist and a owner of Modix BIG-60: “This is the finished print of a cannon for an upcoming production. It’s 5’2″ in length, made up of 12 pieces. Everything fits nicely. It took 108 total print hours (the printer ran day and night). I used a 0.8 ruby nozzle and a 0.4 layer height on detailed parts with a 0.44 layer height on long tube sections. The 2.5 kg rolls were a great success. I was getting approximately 30hr of print time between roll changes.” The video on the right shows the printed canon shooting pyrotechnics.
Metal Cast
1. Print the models in parts and glue them together.
Serdar Eraol, owner of Efes Bronze: “We print with PLA . The bed temperature is 55oC. The print layer is 0.3mm at the base, 0.2mm for the body parts and 0.1mm for the face. We use the 0.4mm nozzle and 7-8% infill. After 100-150 layers, we change the infill to 2-3% only. Some parts are 3 perimeters and some just 2″ Check their Instagram at: instagram.com/efesbronze/
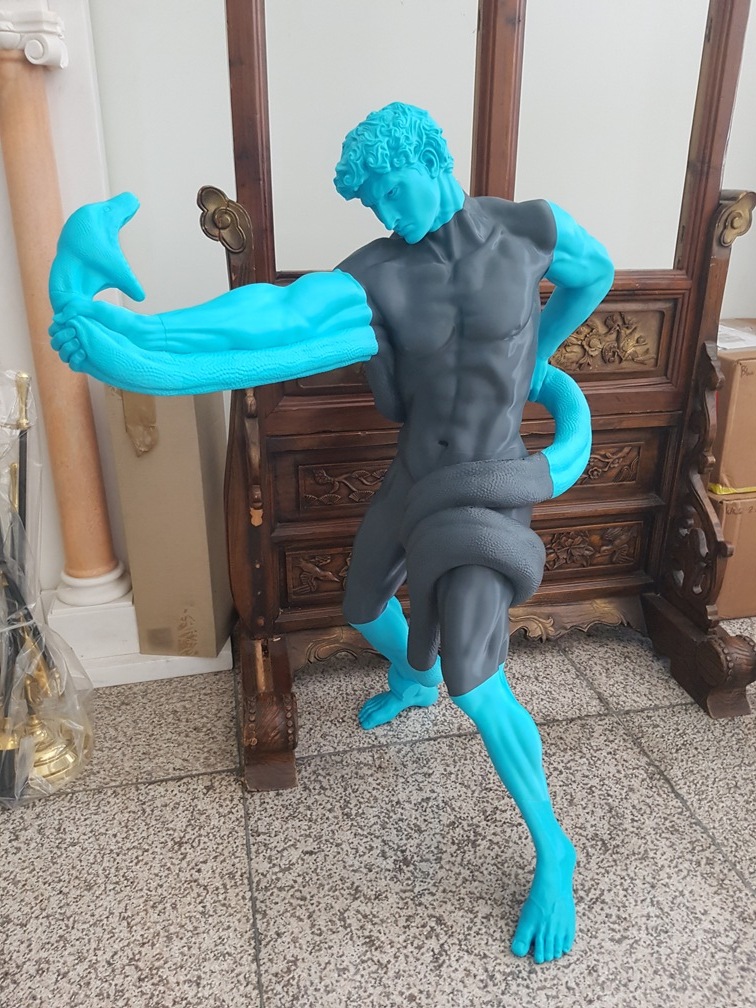
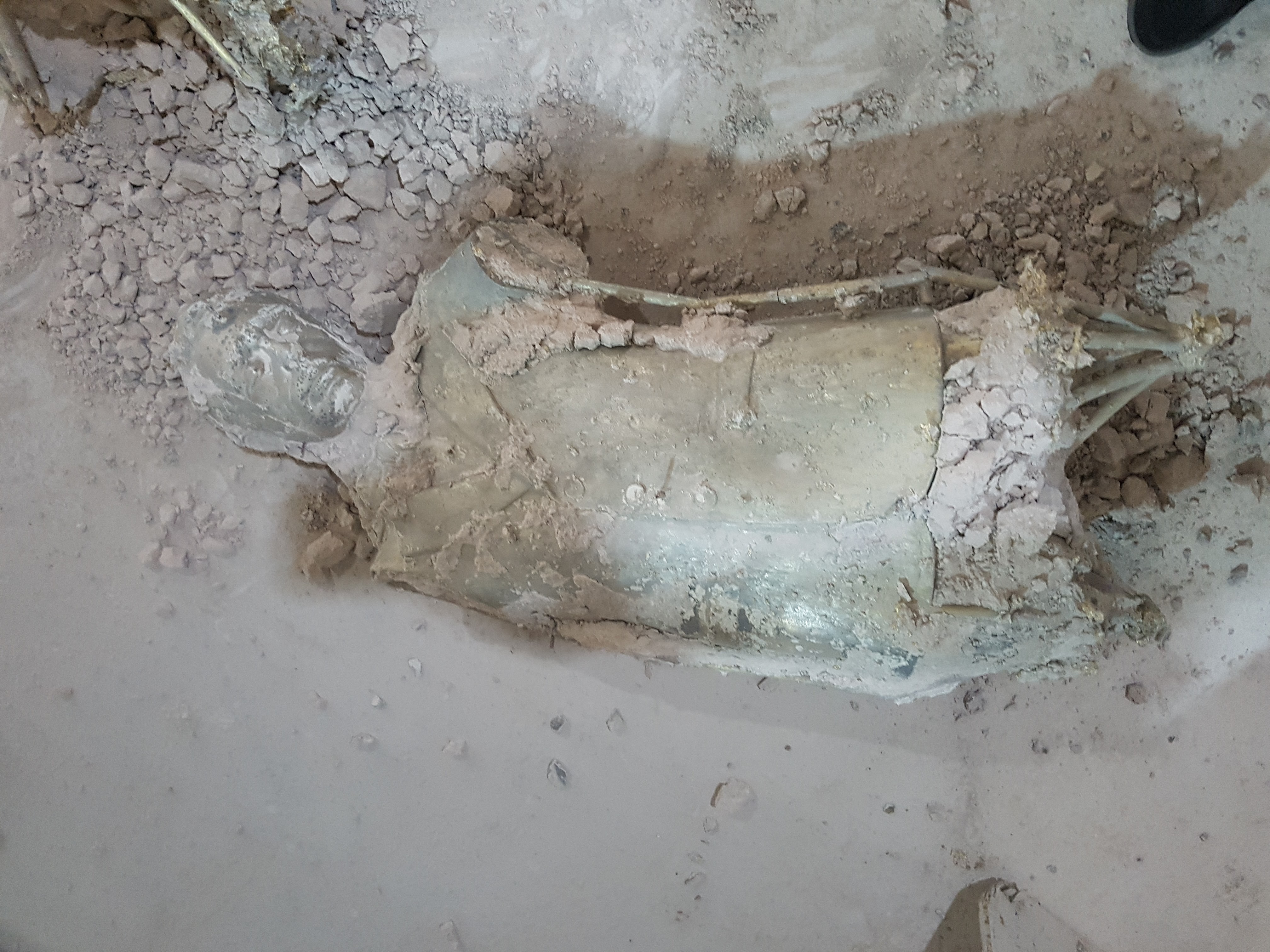
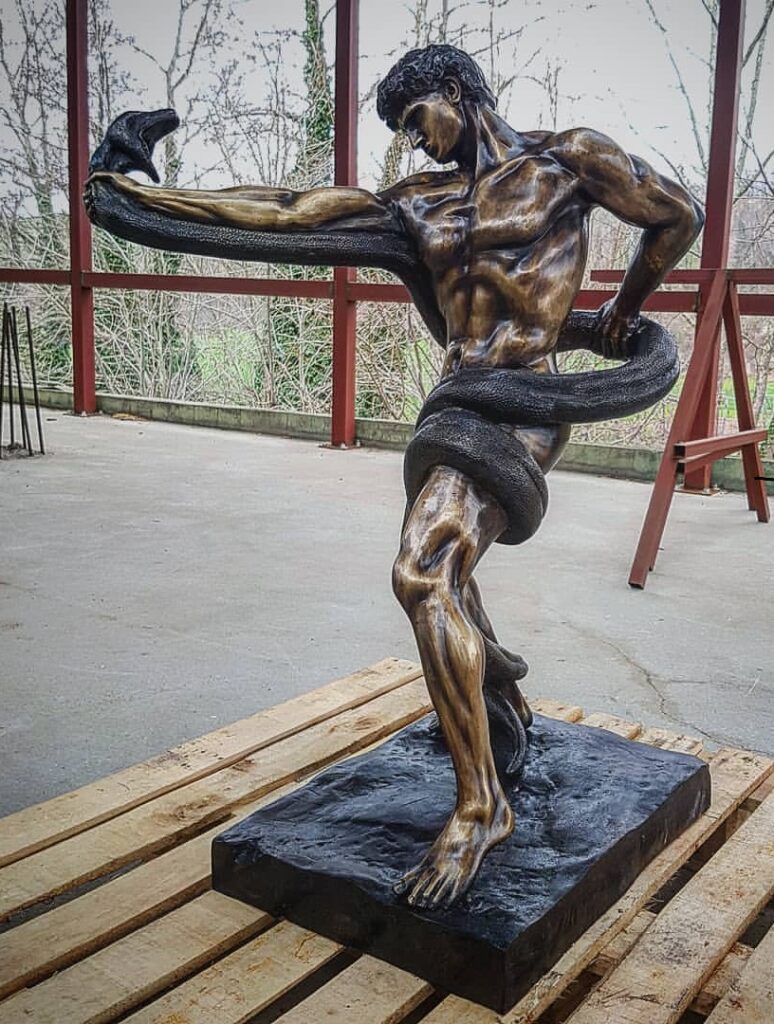
Composite Fabrication Jigs
Several of our customers are using Modix Big 60 to print molds for composite materials, such as carbon fiber. In this example, the printed parts were being used as a jig for precise drilling of a carbon fiber part. Mr. Neal Crookston, Production Supervisor: “The fixtures in the carbon fiber part allows us to fixate it so that we can always accurately drill holes. It took about 60 hours each at 80 mm/s, PLA. The solid one is about 2.5 lbs. of plastic, the one with holes about a pound less.”
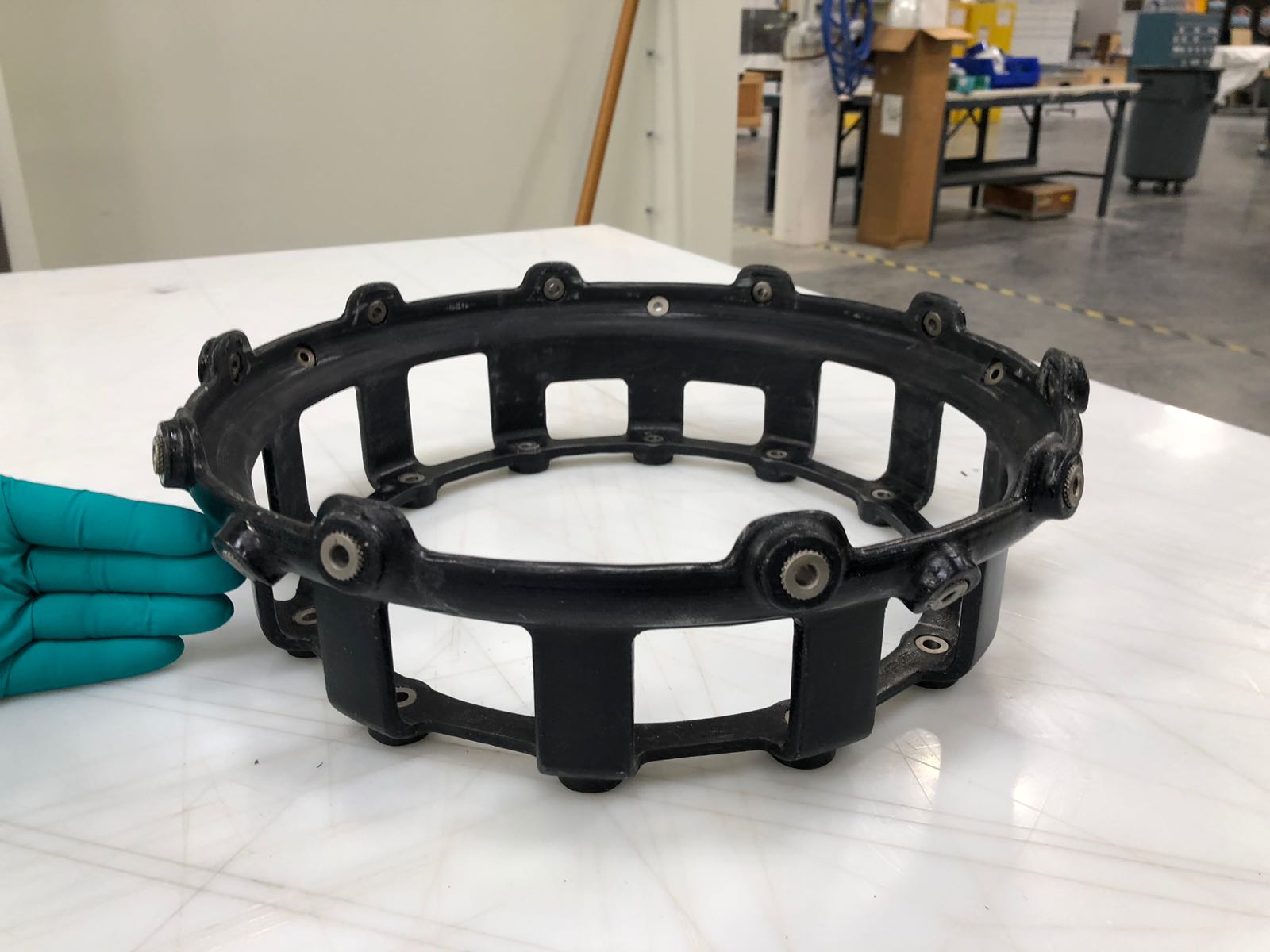
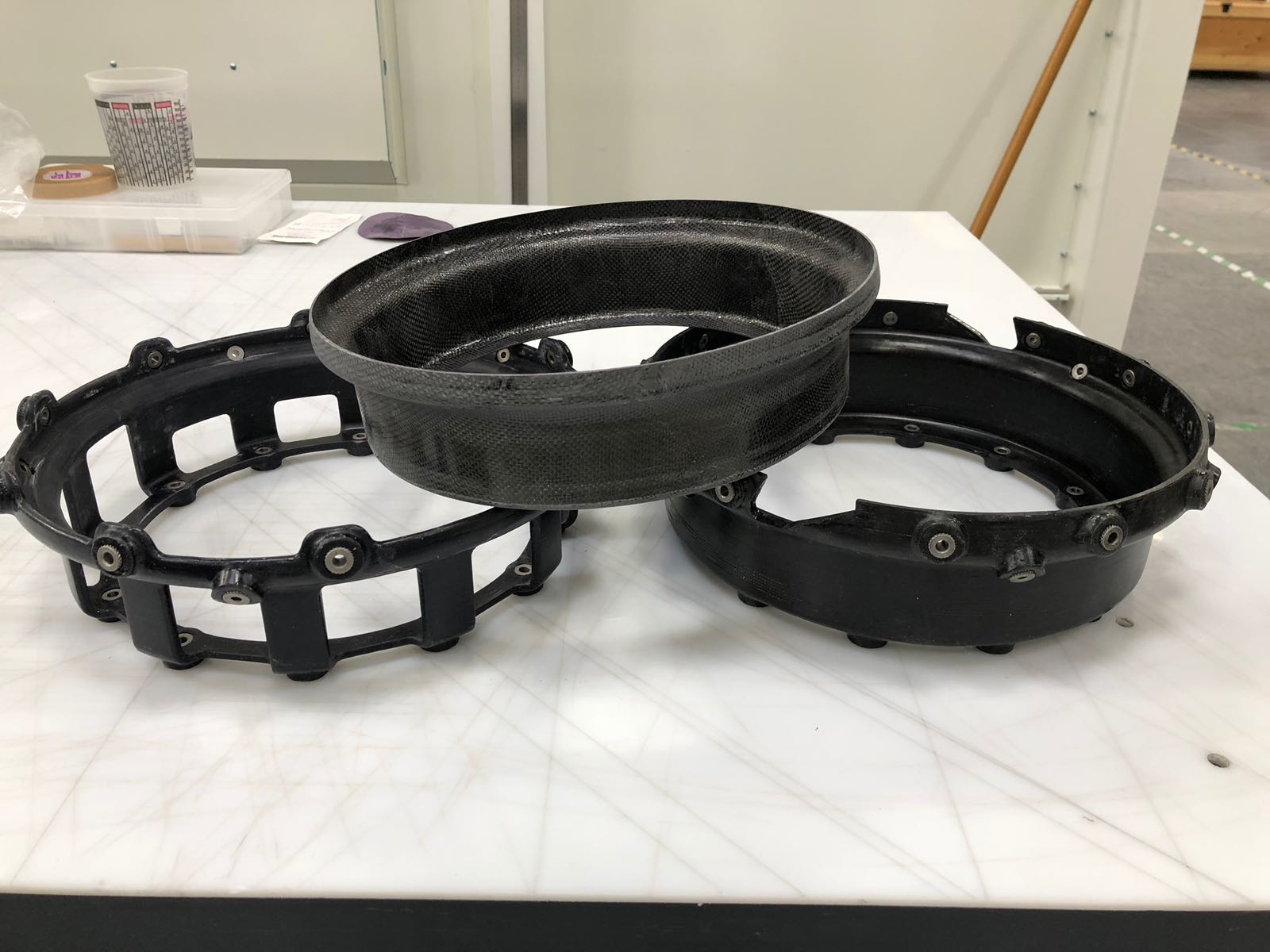
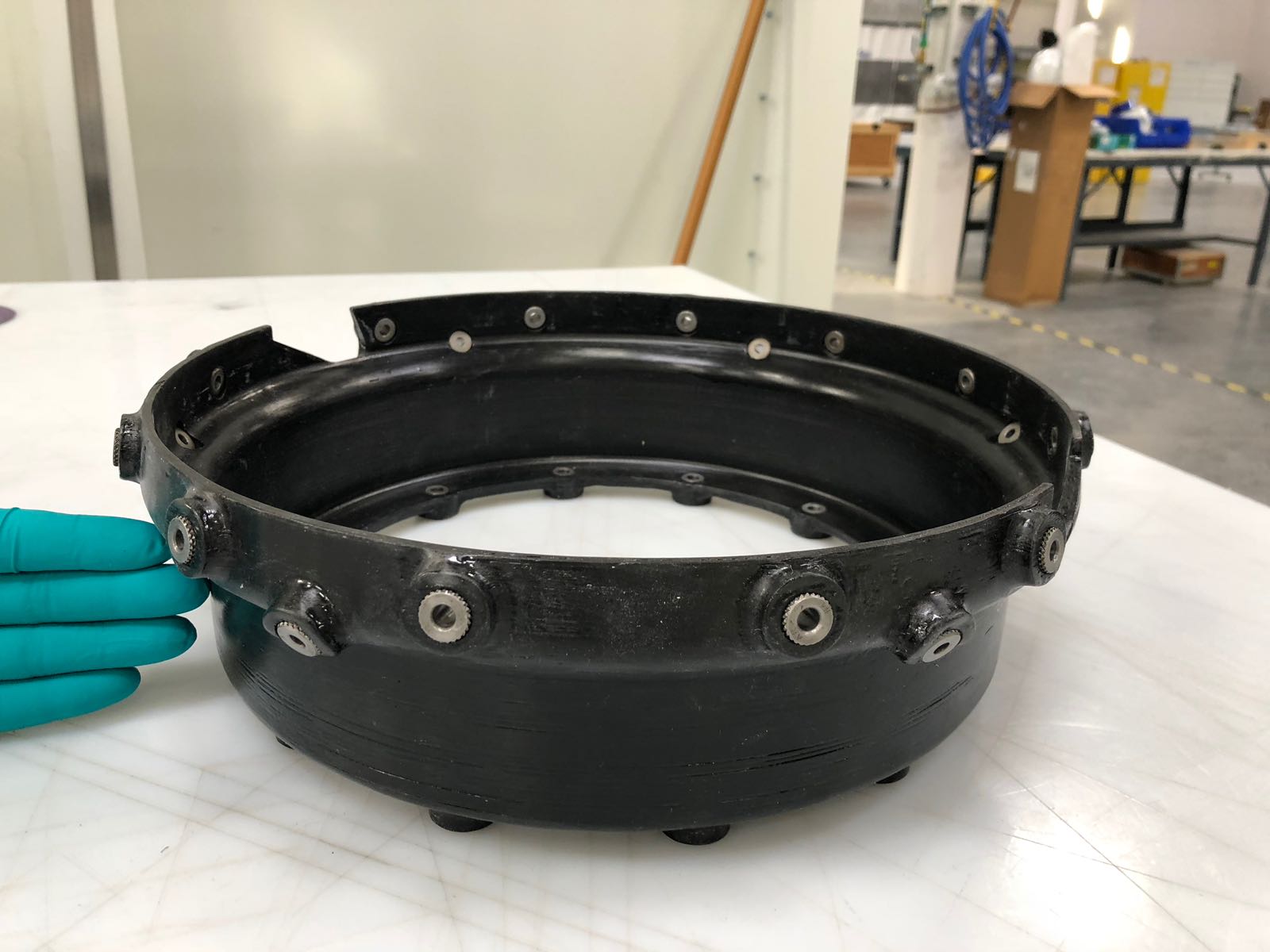
Prosthetics
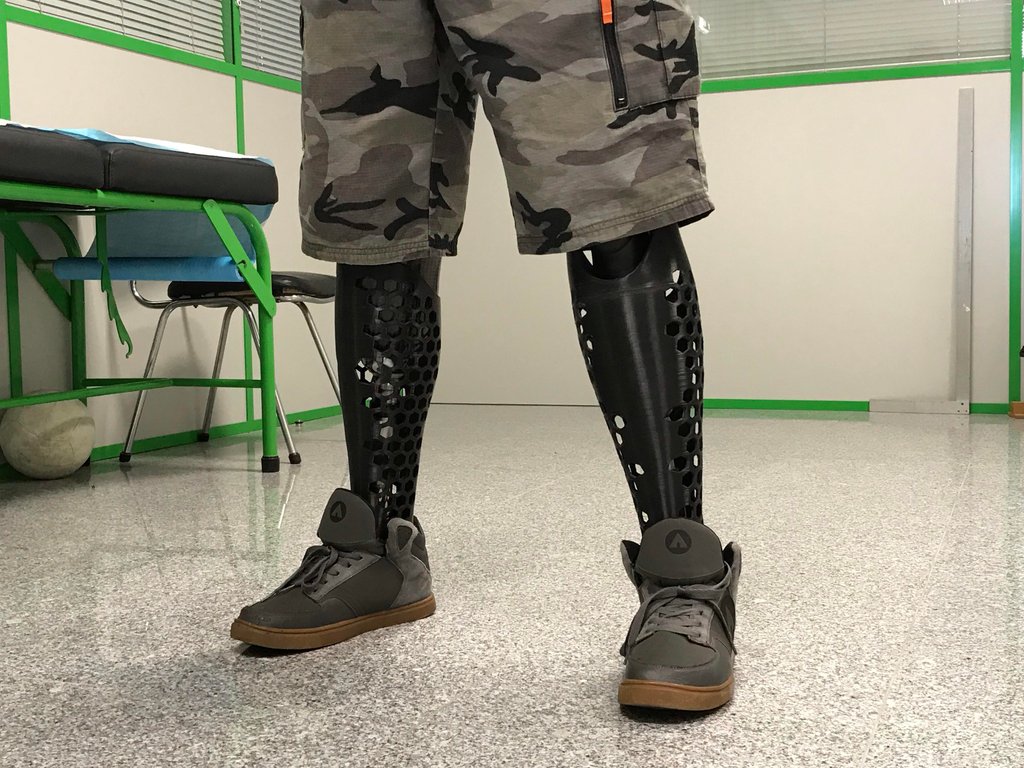
Advertising Props
The advertising market is an avid user of the Modix’s Large 3D printers, mainly for marketing purposes. In this print demonstration, Mr. Craig Tharpe from the USA shows the capabilities of the Big-120X when printing large, impressive models.
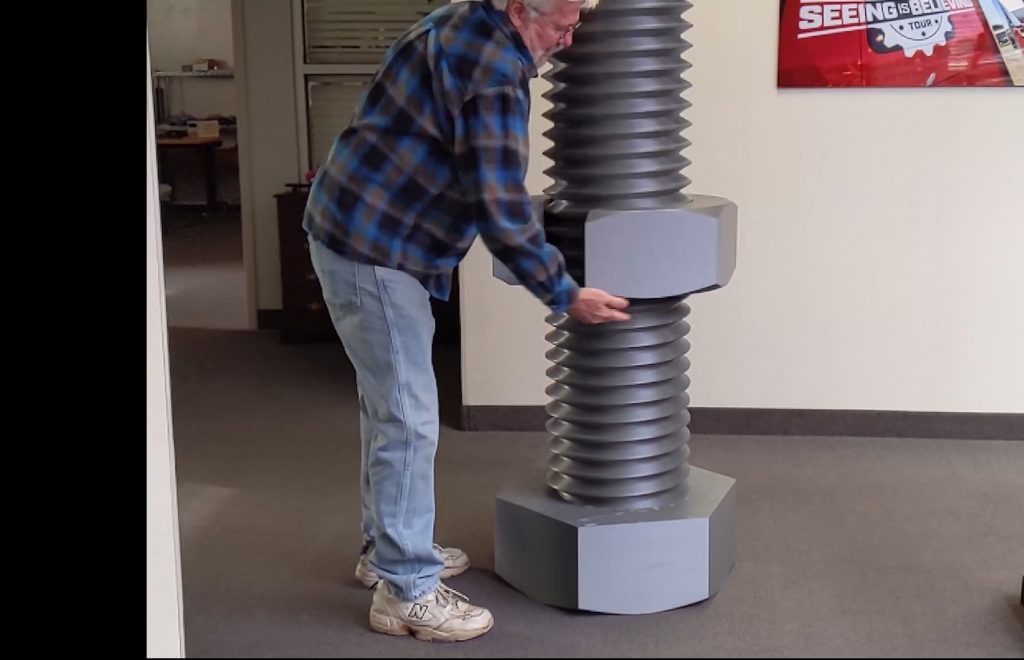
Industrial Scuplting
In a workshop in Hem, Netherlands, Martijn and Dylan have started an adventure that brought together their passion for interior design and technology. Both had a background in interior design, but their dreams extended beyond traditional methods.
Powered by Modix large 3D printers, they are specialized in substantial 3D printing projects for events and commercial needs, creating complex structures up to a cubic meter in one go. Their portfolio features unique creations like a life-sized World War II pilot and custom mascot heads. https://xl3dprinten.nl/
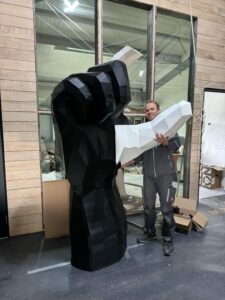
Props
in This video it was demonstrated on how you could make a backup or copy of existing full size commercial sculpture.
Manikins
This showcase highlights the seamless creation of life-sized, anatomically precise manikins, ideal for medical training, fashion design, and retail display. With Modix’s advanced capabilities, users can customize every detail, ensuring that each manikin meets specific needs while reducing production time and costs