Understanding Pellets for Pellet 3D Printing
Pellet 3D printers, also known as Fused Granulate Fabrication (FGF) printers, offer unique advantages in terms of material flexibility and cost-efficiency. When selecting pellets for 3D printing, it’s crucial to understand the differences and implications of various types of pellets available on the market. This article addresses several key aspects: compound vs. virgin grade pellets, recycled plastic vs. virgin plastic, mechanically recycled pellets vs. chemically recycled pellets, and the concept of masterbatch and its use in 3D printing.
Compound vs. Virgin Grade Pellets
Virgin Grade Pellets: Virgin grade pellets are made from raw, unprocessed plastic resins. These pellets are known for their consistency and high quality, making them ideal for applications requiring precise mechanical properties and appearance. Since they are free from contaminants and previous processing histories, virgin pellets ensure optimal performance and reliability.
Compound Pellets: Compound pellets, on the other hand, are mixtures of virgin resins with additives or other resins to achieve specific properties. These additives can include colorants, stabilizers, flame retardants, and reinforcements such as glass fibers. Compound pellets offer tailored properties for specialized applications, but they might come at a higher cost compared to virgin pellets due to the added processing and material costs.
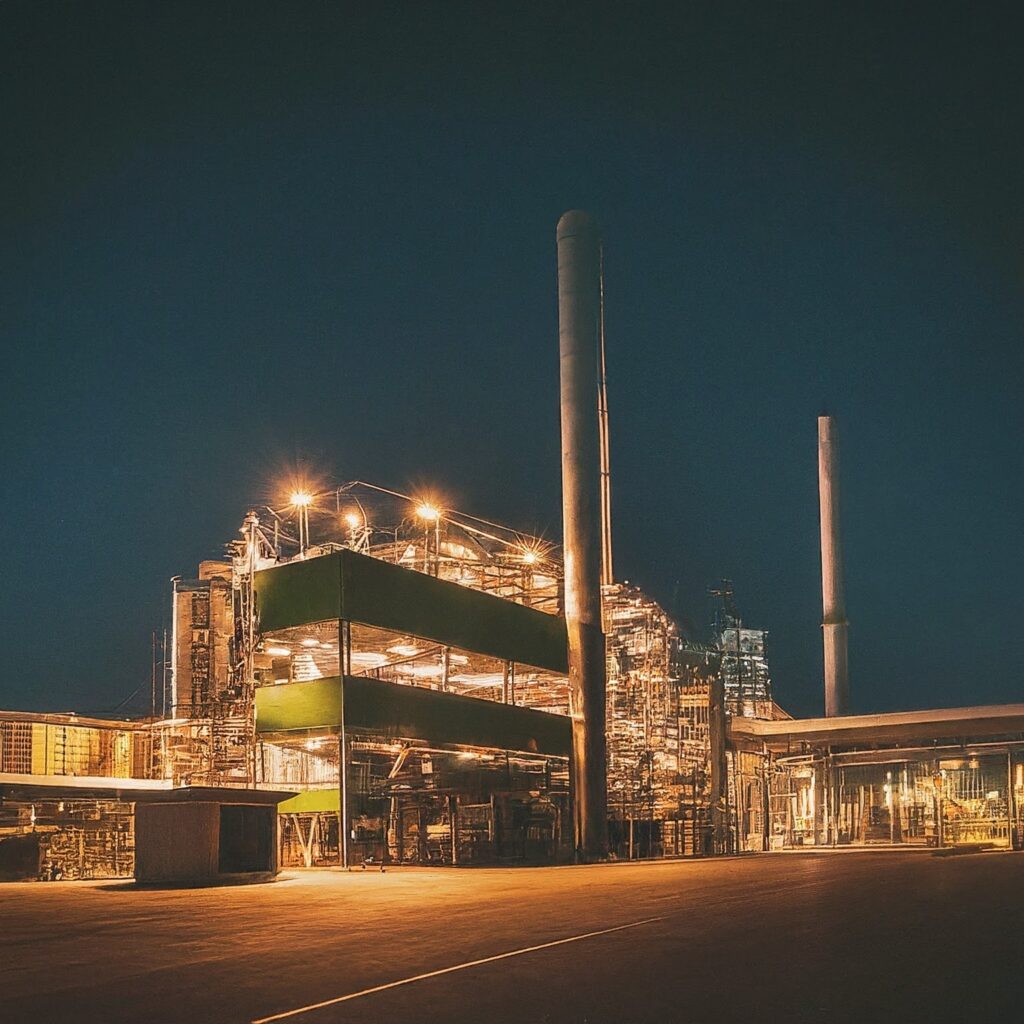
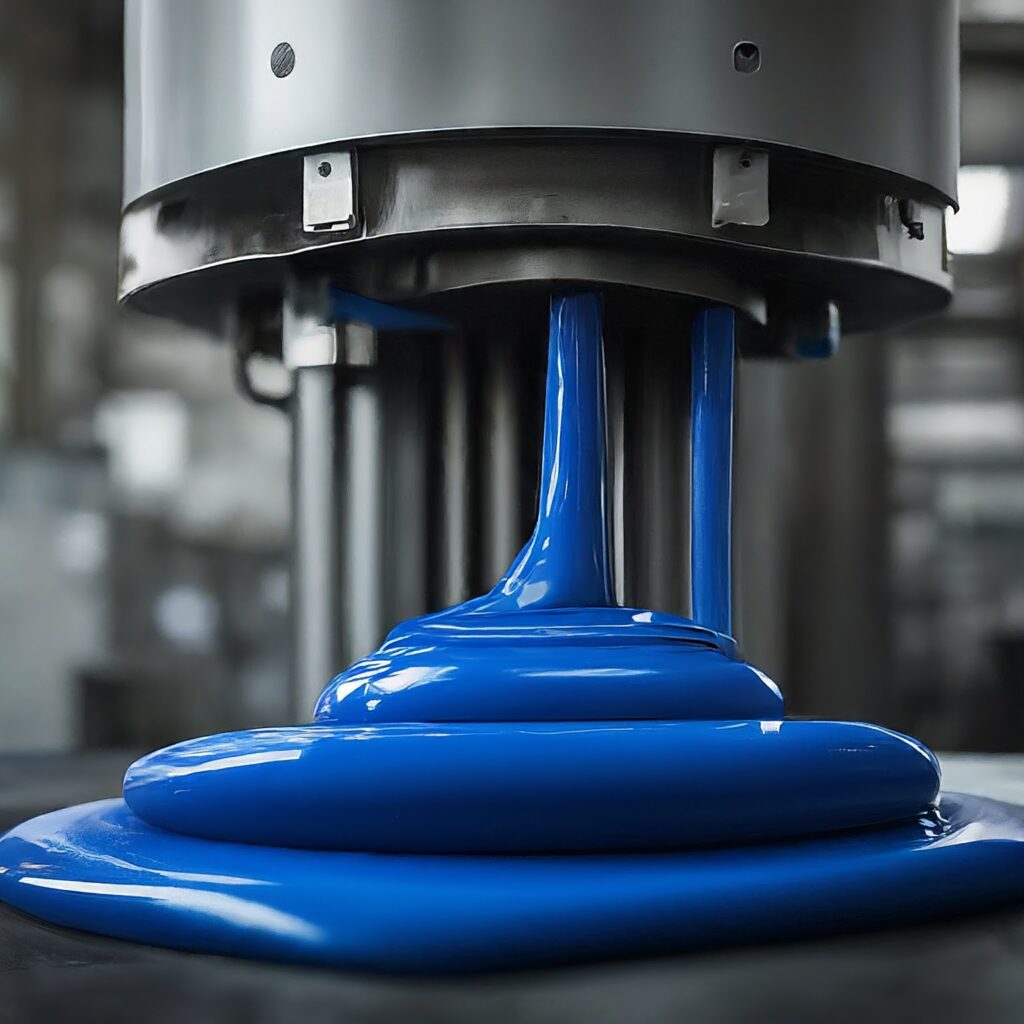
Recycled Plastic vs. Virgin Plastic
Virgin Plastic: Virgin plastics are produced directly from petrochemical feedstocks like natural gas or crude oil. They offer superior quality and performance, with consistent properties that are essential for high-precision applications. However, virgin plastics are more expensive and contribute to higher environmental impact due to the extraction and processing of raw materials.
Recycled Plastic: Recycled plastics are derived from post-consumer or post-industrial plastic waste. These plastics are reprocessed and formed into pellets, which can be used again in manufacturing. The main advantages of recycled plastics are cost savings and environmental benefits, as they reduce the need for new raw materials and help in waste management. However, recycled plastics might have variable properties and potential contaminants, which can affect the quality and performance of the final product.
Mechanically Recycled Pellets vs. Chemically Recycled Pellets
Mechanically Recycled Pellets: Mechanical recycling involves the physical reprocessing of plastic waste into pellets. This process includes shredding, washing, and melting the plastic before reforming it into pellets. Mechanical recycling is cost-effective and widely used, but it often results in materials with lower mechanical properties compared to virgin plastics due to degradation during processing.
Chemically Recycled Pellets: Chemical recycling breaks down plastic waste into its chemical constituents through processes like pyrolysis, gasification, or depolymerization. The resulting monomers can be purified and polymerized to form new, high-quality plastics. Chemically recycled pellets can have properties comparable to virgin plastics, making them suitable for high-performance applications. However, chemical recycling is more complex and expensive compared to mechanical recycling.
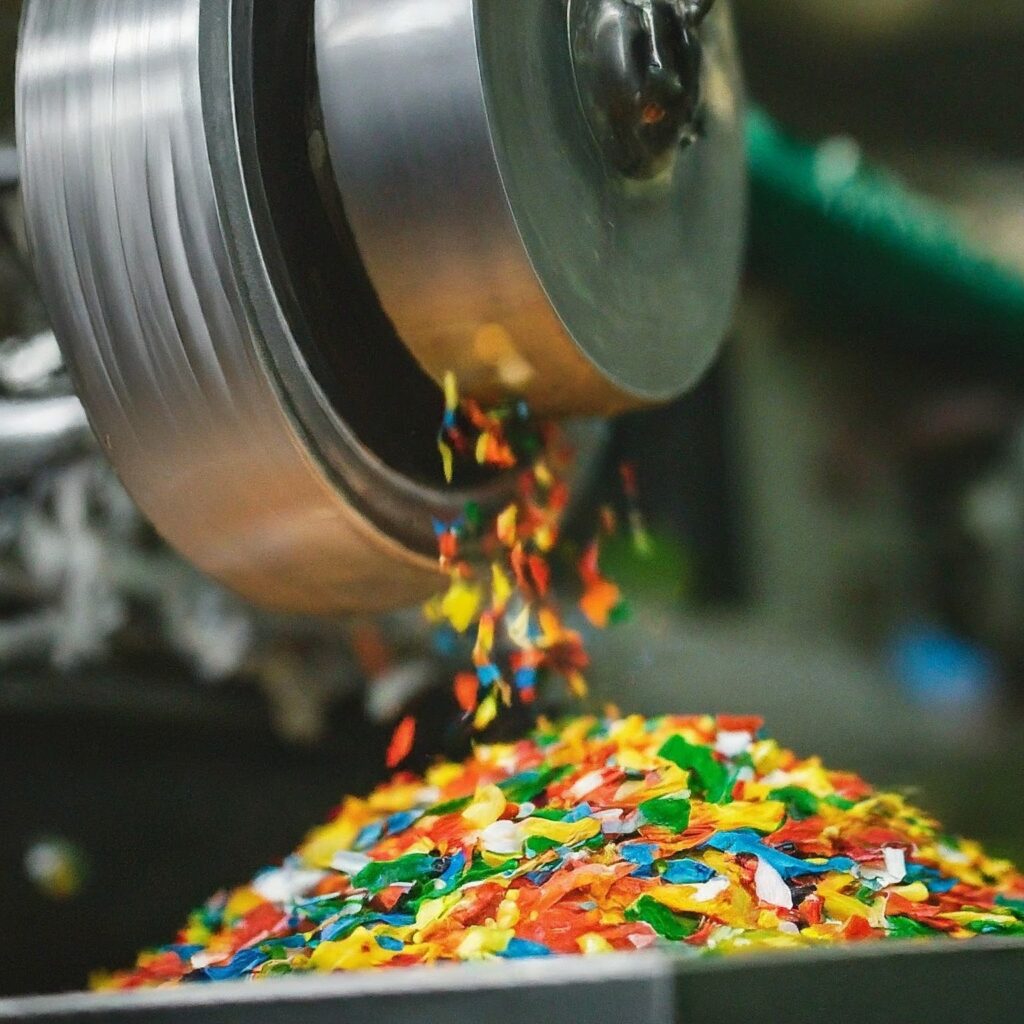
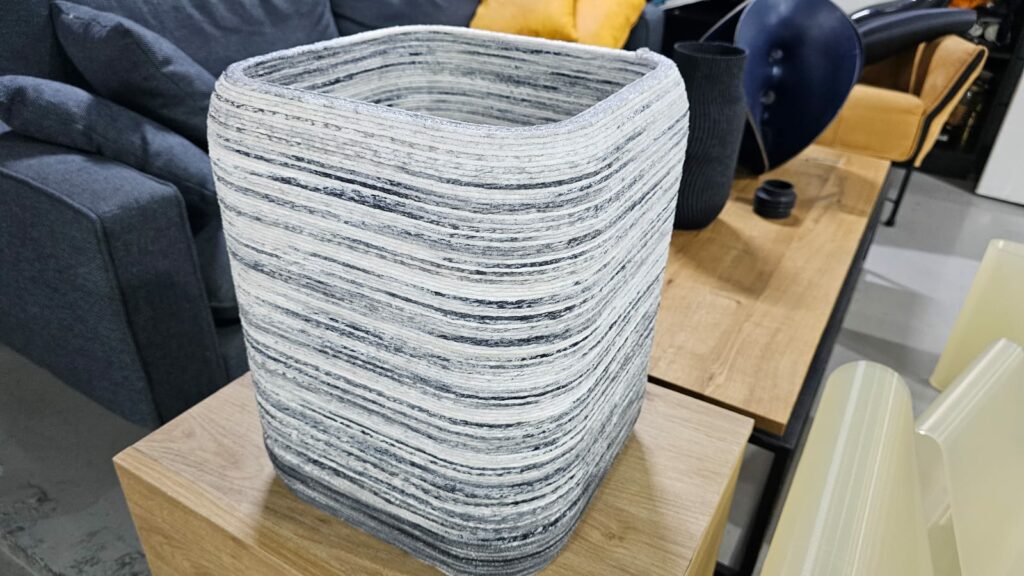
3D Printed by Modix MAMA-1700 with virgin PLA and a mixture of two different Masterbatch, white and black.
The colors are not mixed into a solid grey, instead they generate this pattern effect.
Masterbatch: Definition and Use
What is a Masterbatch? A masterbatch is a concentrated mixture of pigments, additives, or other compounds encapsulated in a carrier polymer. It is used to impart specific properties or colors to the base polymer during processing. Masterbatches come in pellet form and are mixed with the raw polymer resin in precise ratios to achieve the desired effects.
Components and Mixing Ratios:
- Carrier Polymer: The carrier polymer in a masterbatch must be compatible with the base polymer to ensure proper dispersion and performance. Common carrier polymers include polyethylene (PE), polypropylene (PP), and polystyrene (PS).
- Mixing Ratios: Masterbatch is typically added to the base resin in small percentages, often ranging from 1% to 5%, depending on the required intensity of the effect or color.
Applications in 3D Printing: In 3D printing, masterbatches are used to modify the properties of the printing material. For example, a color masterbatch can provide a consistent color throughout the printed object, while an additive masterbatch can enhance properties such as UV resistance, flame retardancy, or mechanical strength. The use of masterbatches allows for customization and optimization of the printing material to meet specific application requirements.
Conclusion
Understanding the differences between various types of pellets and their applications is crucial for optimizing 3D printing processes. Virgin and compound pellets offer different benefits, with virgin providing consistency and compound offering tailored properties. The choice between recycled and virgin plastics involves trade-offs between cost, quality, and environmental impact. Mechanical and chemical recycling methods each have their advantages and challenges, influencing the properties of the recycled pellets. Finally, masterbatches play a vital role in customizing the properties of the printing material, making them indispensable for achieving desired performance characteristics in 3D printed products.
For more information about Modix’s Pellet 3D printer, please visit the product page at: https://Modix3d.com/mama-1700
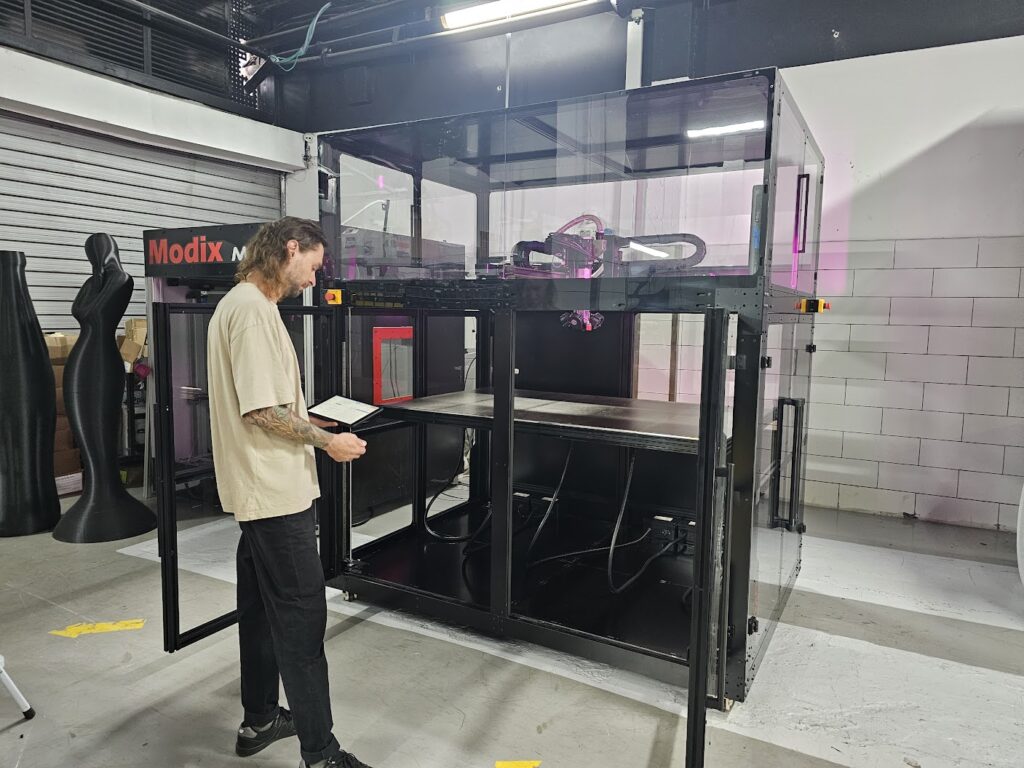