Case Study
Case Study -Preserving History in Full Scale; FloatScans Innovative 3D Scanner
The Company
FloatScans is an Amsterdam-based 3D scanning startup. The company has developed a unique, human sized 3D scanner that captures an objects’ geometry, color and interaction with light, and creates a new dimension for digital experiences and real-world realism. The company provides endless new interactive stories, by digitally preserving art relics and historical items for future generations. Its main clients are museums, private collectors, and auction houses.
The Challenge
FloatScans faces a dual set of challenges where large-scale 3D printing proves indispensable:
- The 3D scanners are deployed in varied physical locations, each with unique requirements for space, positioning, and size. Consequently, scanner parts are custom-made using Modix machines to optimize their functionality.
- The artifacts to be replicated often match human dimensions. This necessitates a printer with substantial build capabilities for rendering such relics and replicas.
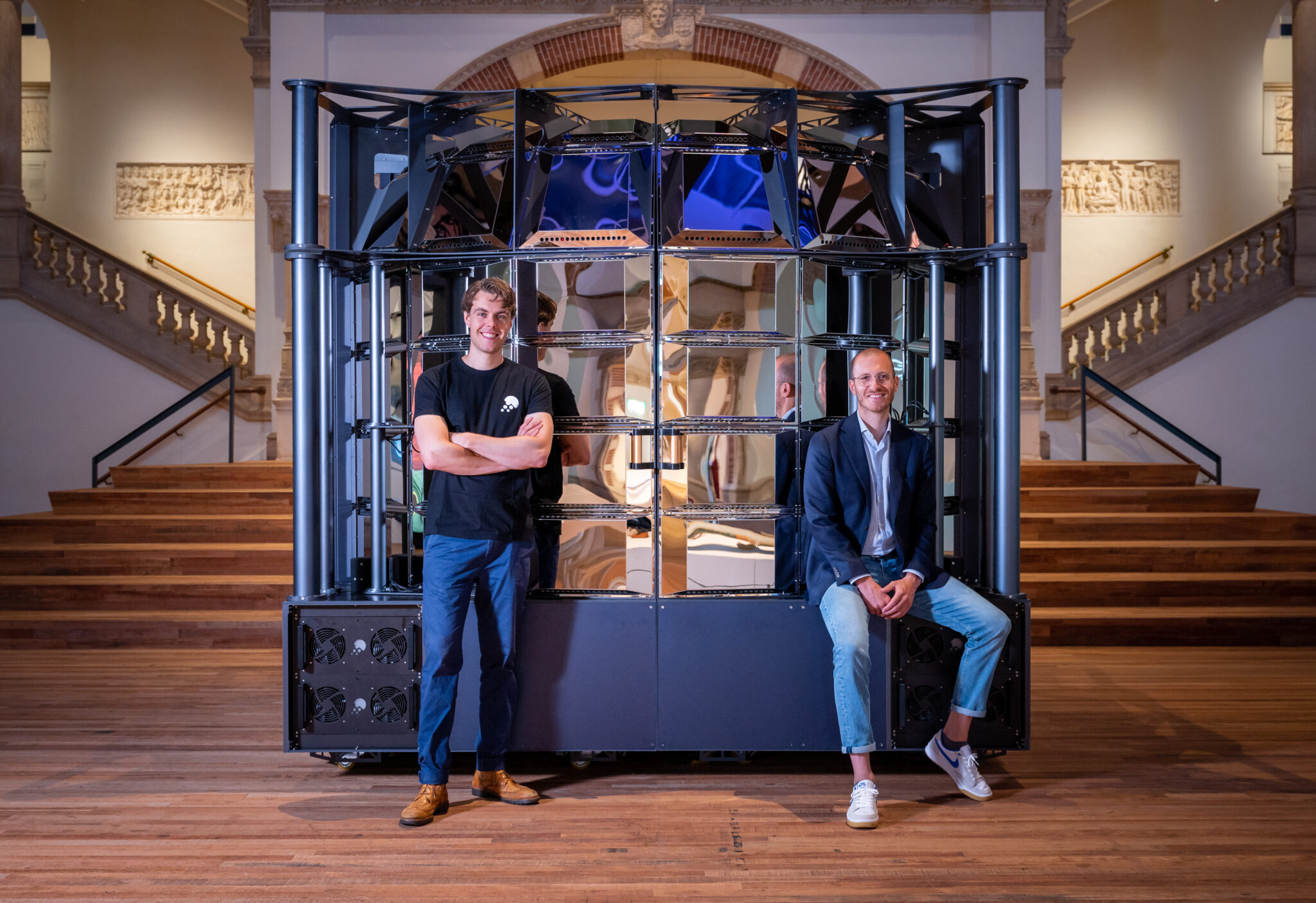
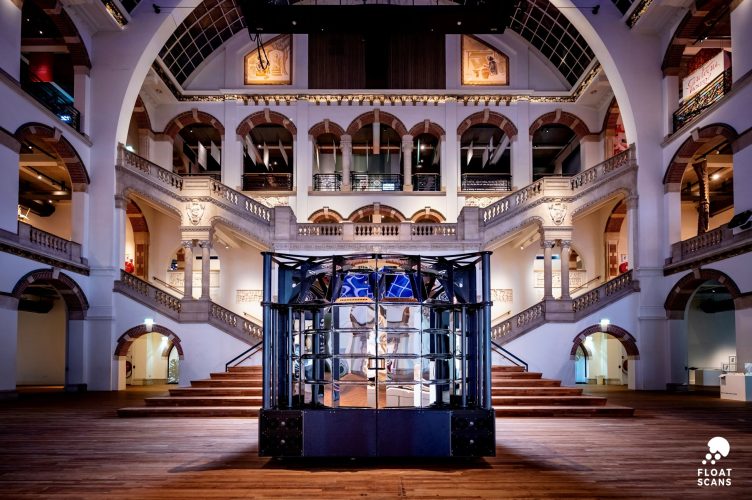
“With Modix, prototyping reduced turnaround time - sometimes within a day - we got a new version in the hands of the engineer. In terms of material we don't even need to make metal parts” says Max Roest, FloatScans’ CEO.
The Solution
FloatScans invested in both the Modix BIG-60 and Big Meter printers to meet these challenges. The company employs these machines for:
1. Engineering and fabricating essential components of their 3D scanners, sometimes producing parts as large as 600 millimeters.
2. Producing a variety of smaller parts in larger quantities, such as unique cable management solutions or hooks.
3. Creating life-sized or larger-than-life relics and sculptures, thereby diversifying its business offerings and accepting more projects.
Max Roest, CEO of the company ,explains the prototyping advantages of using Modix 3D: “For prototyping – we went as far as skipping a manufacturing stage. For example, we’ll need to create a new housing for some complex components, which is pretty difficult. Typically, we would create a first version to see how the tolerances work, and if the components actually fit nicely or we need some adaptations or some margins – we just change it. With Modix, prototyping reduced turnaround time – sometimes within a day – we got a new version in the hands of the engineer. In terms of material we don’t even need to make metal parts. The PLA prints already give enough structural rigidity to hold stuff in place. The plastic part is more than sufficient for us to work with”.
Information box:
Company: FloatScans, The Netherlands
Application:3D Scanning, Digital
Inventory, Prototyping,
Art & Design
Vertical: Mechanical , Engineering
Creative Industry & Arts.
Product development Architecture ,Art
Printers: BIG-60, Big Meter