Case Study:
Bronze Sculpturing Made Easy – Efes Bronze
The Company
The Challenge
The Solution
The Solution
Efes Bronze is using the large print volume of the Modix BIG-60 to print large models (in large parts or in one piece), which are then glued together, covered with silicon in order to create the mold, filled with wax that later smoothed, detailed, and covered in plaster before finally being cast in bronze using the lost-wax technique.
In addition, the Modix BIG-60 printers are reliable and easy to use, which saves Efes Bronze time and money.
In conclusion, Efes Bronze is now able to create large, high-quality bronze sculptures with greater precision and accuracy, using the Modix BIG-60 printers.
How it works
1) Model Creation:
A model is printed using the Modix BIG-60 3D printer. This model is then covered with silicone to create a flexible mold, capturing all the fine details.
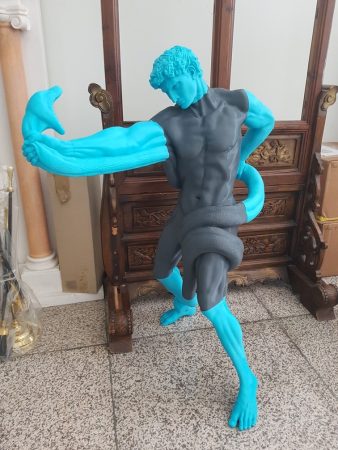
2) Wax Casting:
Wax is poured into the silicone mold and allowed to harden, forming a detailed wax replica of the original printed model. Any final details are added to this wax cast to ensure precision in the final piece.
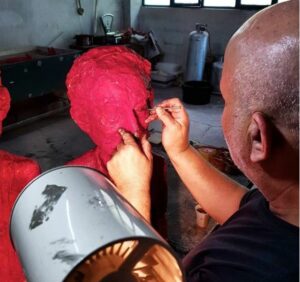
3) Bronze Casting: The detailed wax model is then encased in plaster to create a solid mold. Once the plaster hardens, the wax is melted out in a process known as the “lost-wax” technique, leaving a hollow cavity. Molten bronze is then poured into this cavity, and once it cools and solidifies, the plaster mold is broken away to reveal the final bronze sculpture.
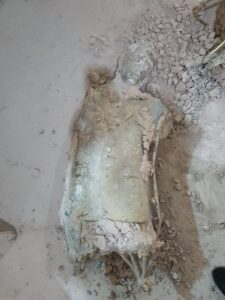